Interview with researchers 1 Nanoscale patterns and natural shapes are leading to new highly functional materials
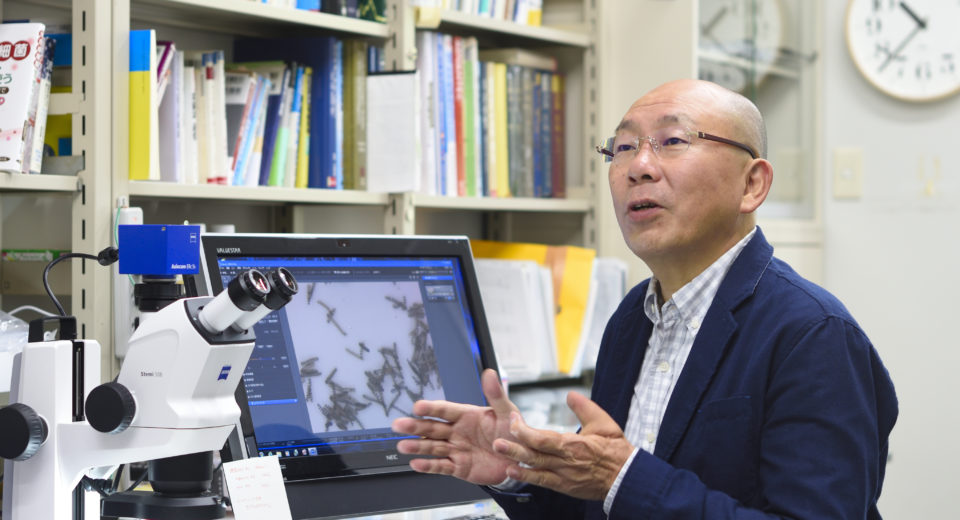
- Interview Tomokazu Iyoda
- Professor, Harris Science Research Institute
Mass production process of metal microcoils derived from coiled algae, Spirulina
Today, polymers such as plastic and synthetic fibers are used for many products that support our daily lives, from daily necessities to clothing and electrical appliances.
Polymer science has made remarkable progress to meet the changing needs of society. Prof. Iyoda is one of the world’s leading researchers in the development of these materials, and is exploring innovative functions using his own methods.
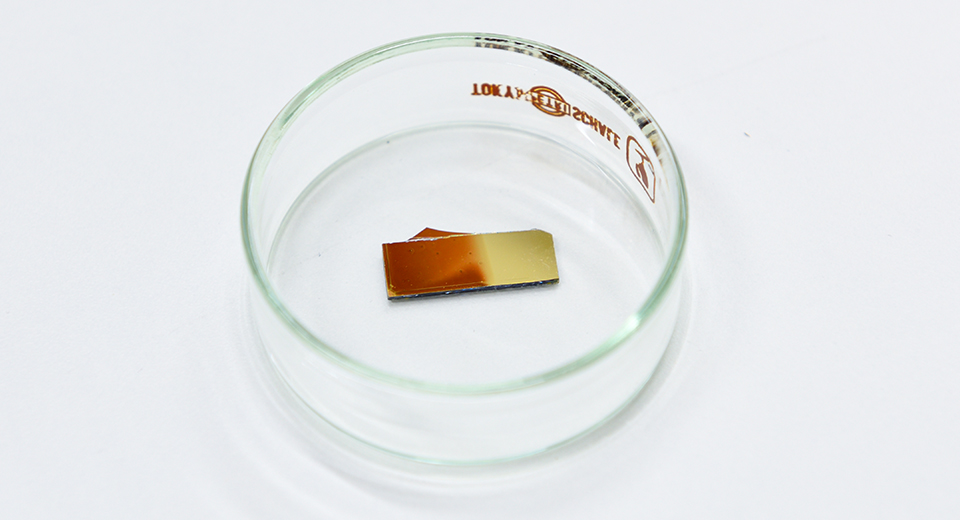
“I have found clues to the fine structure of living things,” he said. He is conducting bio-template research on directly transferring the three-dimensional microstructures of organisms that are difficult to mass-produce, to different materials. One example is a new material called a metal microcoil, which uses the shape of Spirulina.
“We made a metal microcoil by plating the spiral microalgae Spirulina as a mold and metallizing the surface. Plating is a well-established technology, and it is also an elemental technology which can faithfully transfer nanoscale fine uneven structures.“ Metal microcoils have also been established for mass-production processes utilizing the properties of cyanobacteria Spirulina that grows by photosynthesis. “Spirulina is the ultimate template produced solely from sunlight and carbon dioxide. Furthermore, through our research, we found that metal microcoils have good electromagnetic response characteristics.”
It has been proved that dispersion sheets containing metal microcoils have excellent radio wave absorption and shielding properties even in the millimeter-wave and terahertz-wave bands, which are the next-generation communication bands, where the absorption efficiency of conventional magnetic materials is reduced due to their unique fine shape.
With the development of the digital society, people are making greater use of devices that emit electromagnetic waves, such as smartphones and personal computers, and so it will become increasingly important to prevent harmful effects such as radio wave interference and health damage. There are high expectations for the newly developed metal microcoils in the modern age with electromagnetic waves.
Creating innovative membranes The relationship between water and oil provides a clue
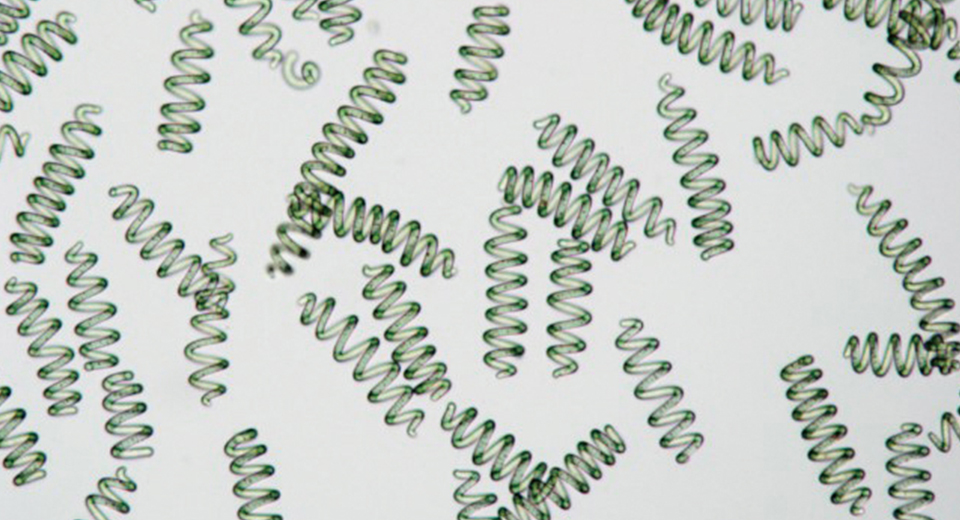
The relationships between persons whose personalities and preferences do not match at all can be likened to water and oil, which are physically immiscible. This is because both water molecules and oil molecules naturally gather together in the same molecule, so molecules with different structures are automatically separated.
When this repulsive property is incorporated into a molecule, a nanoscale ordered structure forms naturally by self-organization. Prof. Iyoda applied not only the transcription of the physical structure of the living body but also such natural providence to material development.
“We discovered that by combining polymers with different properties that do not mix with each other at a single point, they spontaneously show a regular microphase separation structure with a period of several tens of nanometers. Through measures such as the introduction of liquid crystal and heat treatment, we succeeded in creating a film with 10-nanometer-diameter vertical ‘cylindrical’ structures arranged at equal intervals and high density.” This revolutionary thin film has the world’s highest-quality vertically aligned PEO cylinder structure, and has been proven to be a self-organized nano-ordered structure that can be used in engineering. “By synthesizing a block copolymer using a hydrophilic polymer and a hydrophobic polymer, it is possible to create a permeable membrane in which only the contents of the cylinder are made hydrophilic, and by adjusting the production process, we can freely control the diameter and length of the cylinder.”
Because the film is made based on a rational design, it can be reworked flexibly according to the detailed needs of users, and it can be applied in a wide range of situations, such as in medical settings that require filtering of fine components. “Currently, we are also proceeding with a nanotemplate process that transfers vertically aligned PEO cylinder structures to ordered metal nanostructures. By improving the mechanical strength, it should be possible to develop inorganic films with vertical through-holes and excellent heat resistance.”
Furthermore, he aims to develop a wider range of applications by providing some samples to off-campus research institutions and companies, as well as to develop membrane kits that can be easily customized by each researcher. “There is a limit to the applications that I can develop on my own, and the material must be easy for users to handle so that it can be widely used in engineering.” If this kit facilitates the development of various applications, industrialization will eventually occur, bringing great benefits to society.
“We discovered that by combining polymers with different properties that do not mix with each other at a single point, they spontaneously show a regular microphase separation structure with a period of several tens of nanometers. Through measures such as the introduction of liquid crystal and heat treatment, we succeeded in creating a film with 10-nanometer-diameter vertical ‘cylindrical’ structures arranged at equal intervals and high density.” This revolutionary thin film has the world’s highest-quality vertically aligned PEO cylinder structure, and has been proven to be a self-organized nano-ordered structure that can be used in engineering. “By synthesizing a block copolymer using a hydrophilic polymer and a hydrophobic polymer, it is possible to create a permeable membrane in which only the contents of the cylinder are made hydrophilic, and by adjusting the production process, we can freely control the diameter and length of the cylinder.”
Because the film is made based on a rational design, it can be reworked flexibly according to the detailed needs of users, and it can be applied in a wide range of situations, such as in medical settings that require filtering of fine components. “Currently, we are also proceeding with a nanotemplate process that transfers vertically aligned PEO cylinder structures to ordered metal nanostructures. By improving the mechanical strength, it should be possible to develop inorganic films with vertical through-holes and excellent heat resistance.”
Furthermore, he aims to develop a wider range of applications by providing some samples to off-campus research institutions and companies, as well as to develop membrane kits that can be easily customized by each researcher. “There is a limit to the applications that I can develop on my own, and the material must be easy for users to handle so that it can be widely used in engineering.” If this kit facilitates the development of various applications, industrialization will eventually occur, bringing great benefits to society.
Exploration and vision are essential for material development
After graduating from Kyoto University Graduate School, Prof. Iyoda has engaged in diverse works at a number of research institutions, but all are characterized by the application of his intellectual curiosity and original ideas to research. “By jumping into various environments and being stimulated, my range of interests expanded, and I was good at concentrating on what I found interesting.” He attracts attention from various fields with his unique research, but always remembers that practicality is indispensable in manufacturing.
“The world of engineering is not just about searching for the truth to elucidate and verify structures and principles. If we cannot develop applications that meet the needs of society and processes that allow mass production everywhere, the material will not be useful in the real world. As researchers, we have a responsibility to create scenarios with added value, because we are creating something that has never existed in nature before.” He is working on the development and mass production of new materials together with various companies and research institutions toward industrialization.
“I was in a laboratory where there was a lot of free and open discussion when I was in graduate school. That academic atmosphere made me aspire to be a researcher. In an atmosphere with much ambition and scientific effort, I realized that research is never enough.” The world of polymers handled by Prof. Iyoda may be on the nanoscale, but the research potential is immense.