Research News: Analysis of Spray Impingement and Wall Film Formation in Direct Injection Engines
August 29, 2024
The study reveals the mechanisms behind wall film formation, a key contributor to particulate matter emissions under cold fuel conditions
Particulate matter emissions from direct injection engines are a major environmental issue. Researchers at DoshishaUniversity studied how wall films, which form when fuel sprays onto engine walls, contribute to these emissions in cold conditions. They found that cold fuel creates thicker wall films, resulting in more particulate emissions. This finding will help develop improved fuel injection methods, making engines cleaner and will help to attain the upcoming Euro 7 emission standards.
The growing concerns about air pollution and its harmful effects on human health and climate change have led to increasingly stringent vehicular emission norms. These regulations have contributed to significant reductions in carbon monoxide, hydrocarbons, nitrogen oxides, and particulate matter from transportation sources. The European Union’s Euro 7 standard, set to take effect in 2026, further tightens these limits by establishing a threshold for 10 nanometer particulate matter emissions and requiring low-temperature emissions testing at -7°C.
To help improve combustion processes and reduce particulate emissions, researchers at Doshisha University have revealed how fuel spray forms wall films inside direct injection engines. Their findings made available online on July 18 2024 in Fuel, provide valuable insights into the effects of cold conditions on wall film formation and its contribution to particulate matter emissions.
The research team was led by Dr. Dai Matsuda, a former doctoral student at Doshisha University who is now a researcher at the National Institute of Advanced Industrial Science and Technology, and included Jiro Senda and Eriko Matsumura from Doshisha University, Japan.
Direct fuel injection vehicles have gained popularity due to their higher fuel efficiency, with savings of 10 to 20% compared to port injection systems. In 2020, 55% of light-duty vehicles in the United States were equipped with direct-injection engines. However, injecting fuel so close to the engine reduces the time available for fuel to evaporate and mix with air, leading to a richer fuel mixture and increased deposition on cylinder walls. This can result in incomplete combustion and higher levels of particulate matter in the exhaust.
“When a certain amount of fuel is injected, some of it impinges on the wall, some of it adheres to the wall, and the amount of wall film that does not break up is the final amount. Our research aims to clarify the relationship between phenomena and mass in the process of wall film formation,” explains Dr. Matsuda.
To simulate the formation of wall films on engine cylinder walls, the researchers injected isooctane into a wall surface whose temperature and injection pressure could be controlled. Isooctane was chosen because it behaves similarly to gasoline at low temperatures. In the setup, isooctane was injected at a 45-degree angle onto a wall surface through an injector cooled with dry ice. The temperature of the wall surface was regulated using a heat exchanger bonded directly to its sides. The wall surface was then housed in a container sealed with nitrogen to eliminate the effects of moisture present in the air.
The researchers used two methods to measure the mass of fuel spray that adheres to the wall: an absorption method that involves weighing a sanitary napkin placed on the wall after fuel injection, and the Total Internal Reflection Laser-Induced Fluorescence (TIR-LIF) method, which uses a laser to detect fluorescence from markers mixed with the fuel.
The experiments found that as the fuel spray impacts the wall, more fuel adheres to it over time, causing the wall film to thicken. This thickness reaches its maximum by the end of the spray. After this peak, the amount of fuel adhering to the wall drops quickly and then stabilizes. This indicates that the wall film breaks up after the spray has stopped. At a fuel injection temperature of 253 Kelvin (K) (-20.15°C), the spray wall impingement ratio (which is the ratio of the amount of fuel that impinges on the wall to the total amount of fuel injected) increased by 8.4% compared to 293 K (19.85°C). This increase occurs because colder fuel is more viscous and does not atomize as effectively, leading to fewer but larger droplets hitting the wall. However, the larger droplets adhere less efficiently than smaller, more dispersed droplets and eventually fall off the film after the spray has stopped. Additionally, higher injection pressures caused more fuel to splash against the wall, reducing the final amount of fuel adhering to the wall.
“Cold fuel increases the ratio of spray impingement, leading to a higher ratio of wall adhesion,” explains Dr. Matsuda.
These findings provide a detailed understanding of wall film formation, which can aid in optimizing fuel injection strategies and developing cleaner, more efficient direct injection engines.
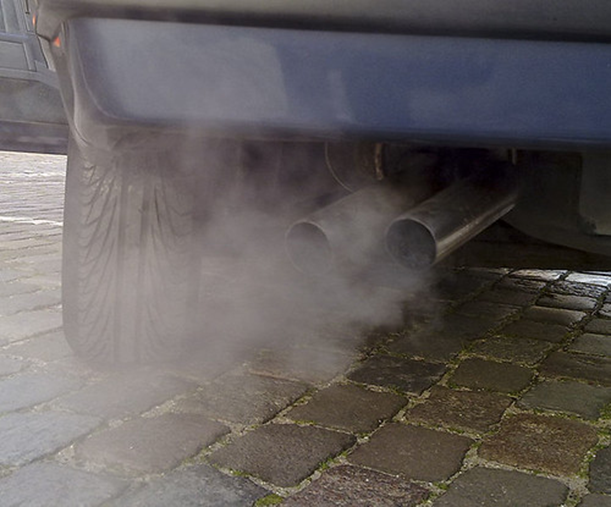
Combatting particulate matter emissions from direct-injection engines
This study investigates the formation of wall films in direct injection engines, a key factor in particulate matter generation. The results show that cold fuel adheres more to the wall creating thicker films, which can increase particulate matter emissions.
Image courtesy: “Car exhaust” by eutrophication&hypoxia
Image license: CC BY 2.0
Usage Restrictions: You are free to share and adapt the material. Attribution is required.
Reference
Title of original paper | Experimental analysis of spray impingement wall film at cold temperatures for Direct-Injection spark ignition engines |
Journal | Fuel |
DOI | 10.1016/j.fuel.2024.132407 |
Funding information
This work was supported by JSPS KAKENHI Grant Number JP22KJ3000. (Grant-in-Aid for JSPS Fellows). The nozzle used in this study was a prototype and was provided by DENSO CORPORATION.
EurekAlert
https://www.eurekalert.org/news-releases/1055769
Profiles
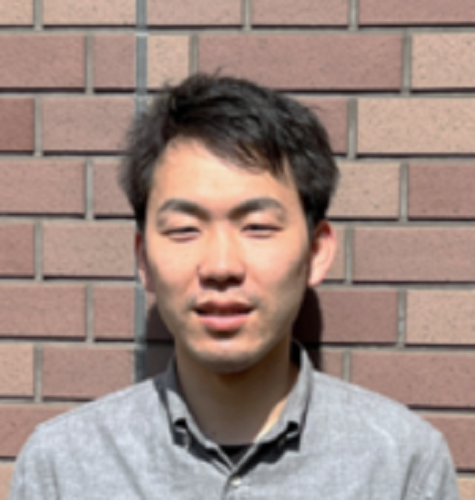
Dai Matsuda
National Institute of Advanced Industrial
Science and Technology
Dai Matsuda is a researcher at the National Institute of Advanced Industrial Science and Technology. He earned his Doctor of Philosophy in Engineering from Doshisha University in March 2024. His research interests include fuel film formation, spray combustion, optical measurement, breakup models, mixture formation, atomization, and internal combustion engines. Dr. Matsuda has received several awards, including the 2023 Graduate Research Encouragement Award from the Society of Automotive Engineers of Japan and the Excellent Presentation Award at the 32nd Symposium on Liquid Atomization. His work has been published in numerous peer-reviewed journals, and he has presented at international conferences. For more information or to contact Dr. Matsuda, please email him at d.matsuda@aist.go.jp
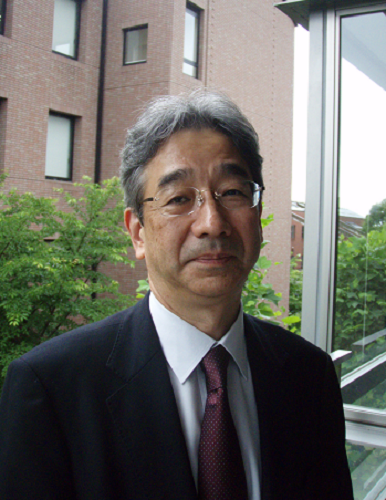
Jiro Senda
Professor, Faculty of Science and Engineering Department of Mechanical Engineering and Science
Jiro Senda is currently a Professor at the Department of Department of Mechanical Engineering, Graduate School of Science and Engineering, Doshisha University. His research focuses include Optical Measurements, Fuels, Spray Dynamics, Spray and Combustion Control for Internal Combustion Engines, Modeling and CFD (Computational Fluid Dynamics), and Sustainable Urban Design with Optimal Energy Application. The Spray and Combustion Engineering Laboratory focuses on the study of thermofluid phenomena, including unsteady reactive flows. Specifically, it deals with atomization and evaporation (phase change) of sprays, diffusion and mixing, combustion and chemical reactions, turbulence in fluids, mixing processes caused by vortex formation, and cavitation phenomena that occur in unsteady liquid pressure fluctuation fields, as well as nucleation processes that govern the occurrence of cavitation.
Media contact
Organization for Research Initiatives & Development
Doshisha University
Kyotanabe, Kyoto 610-0394, JAPAN
CONTACT US